The Low-Down On Sustainable Cotton
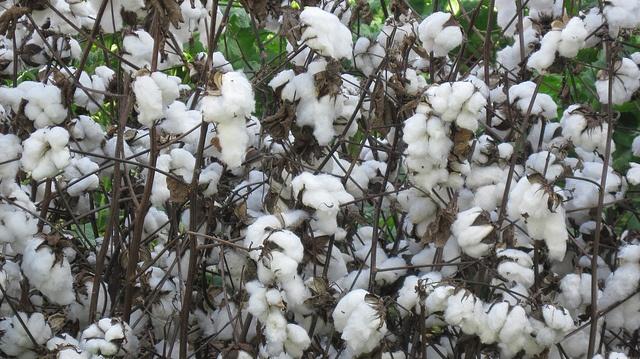
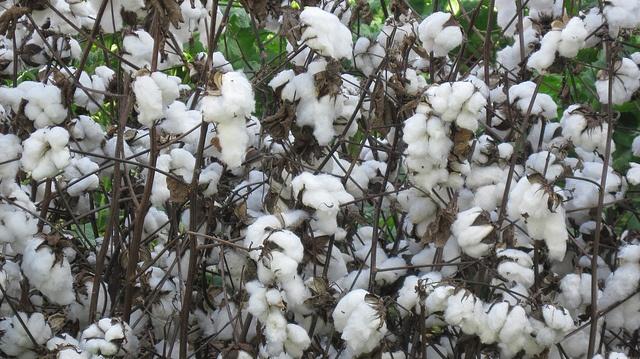
Cotton as a fiber is plant-based and as such is more sustainable than synthetic fibers. It is renewable and supports about 250 million people globally. Worn around the world, over 25 million tons of cotton are produced every year in around 85 countries.
Cotton is approximately 55 percent of the fiber used in clothing and textile production. Over 60 percent of the world’s cotton is grown and produced in developing countries and provides a livelihood for over 100 million farmers. But intensive farming methods are used, such as overusing water and pesticides, and those methods threaten the ecosystems cotton depends on. Cotton farmers are also subject to price fluctuations and increasing input costs. Conventional cotton growing is just not sustainable.
“The indiscriminate use of pesticides is bad for the soil and has human health impacts. It’s generally bad for the community,” Anita Chester, head of sustainable raw materials for the C&A Foundation, told TriplePundit.By contrast, sustainable cotton is “cotton that’s grown carefully” with environmental and economic aspects considered, Chester said. One standard within sustainable cotton is organic, which does not need pesticides or insecticides and uses less water and energy. It’s environmentally friendly and provides financial security for smallholder cotton farmers. Chester explained that with organic cotton production, “natural methods are used to control pests with no GMO seeds used.”
The problem is that organic cotton only accounts for 1 percent of total cotton production. Organic cotton production has actually declined over the last five years. “Farmers don’t see the advantage in staying organic,” Chester said. “They don’t see a business case.” There are other problems, she added. “Retailers face issues of lack of transparency in their supply chains. There’s a huge fear of GMO contamination.”
Consider that India, a developing country, is the biggest organic cotton producer, accounting for 75 percent of all organic cotton globally. Most Indian cotton farmers are smallholders farming less than two hectares of land. Organic cotton production is certainly not easy for smallholder farmers. However, there is another standard, Better Cotton, which “substantially scaled up in the last five years” and is “an easier standard for farmers to follow,” Chester explained.
With Better Cotton, pesticides and insecticides are used, but the principle is “continued improvement.” In 2014, 7.6 percent of all cotton produced globally was Better Cotton, according to the Better Cotton Initiative’s 2014 sustainability report. The initiative wants that amount to hit 30 percent by 2020 because it believes that “will be a tipping point and lead to transformational change for the entire sector.”
Top international brands like H&M and Nike use Better Cotton in their supply chains and their support increases its penetration in the market. H&M is one of the biggest users of organic cotton in the world. The retailer's goal is for all of the cotton it uses in its products to come from more sustainable sources by 2020. It defines more sustainable sources as being “either organic, better or recycled.”
C&A Foundation has a number of initiatives to help overcome the obstacles to sustainable cotton growth. One of those is the Organic Cotton Accelerator, created in 2013 by Textile Exchange, C&A Foundation, CottonConnect and small group of brands to accelerate organic cotton production. A global initiative, it addresses obstacles to organic cotton production and helps link producers to the market.
Connecting retailers with sustainable cotton production is key. In 2009, C&A Foundation, Textile Exchange (formerly Organic Exchange) and the Shell Foundation founded CottonConnect. Since its launch, CottonConnect has helped retailers buy more sustainable cotton grown by smallholder Asian farmers. It has supported over 40,000 farmers in India, China and Pakistan to reduce both their input and water use.
Working with CottonConnect, C&A Foundation organized an event that brought over 170 stakeholders in the Indian organic and sustainable cotton sector together in March 2014. As a result, the Organic and Fair Cotton Secretariat in India was created, and the foundation supports it financially. The group is made up of Indian private-sector champions, NGOs and other stakeholders. Its goal is to raise awareness and be advocates for more supportive policy framework for organic cotton.
The many benefits of sustainable cotton
Sustainable cotton is badly needed. “No commodity is as polluting as cotton,” declares the Sustainable Trade Initiative. About 10 percent of all agricultural chemicals used globally are used by the cotton sector. It's only grown on about 2.5 percent of the world’s agricultural land. The pesticides end up in groundwater and rivers. They not only get rid of pests but also the natural enemies of those pests, and that interferes with the ecosystem.Production of the synthetic fertilizers used in cotton farming use 1.5 percent of the world’s annual energy consumption. They cause other environmental problems. The continued application of nitrates on farm land means they produce nitrous oxide, a greenhouse gas with a warming potential 300 times that of carbon dioxide. And soils contain carbon, so if soils are degraded they are able to sequester less carbon.
Soil health is what Chester considers to be “the most important thing” when it comes to farming. Sustainable practices help the soil while unsustainable ones deplete it. “That’s an area where farmers must use sustainable practices,” she said. Maintaining good soil helps it retain moisture, and that is increasingly becoming a very important aspect of sustainable cotton farming.
Cotton production is an intensive water user. It takes a lot of water to produce cotton, requiring over 20,000 liters of water to produce just one kilogram of cotton, which is equivalent to one T-shirt and a pair of jeans. Most of the global cotton harvest, about 73 percent, is grown on irrigated land, according to World Wildlife Fund estimates. Climate change is affecting farmers. In developing countries like India, cotton is mostly a rain-fed crop. “Weather patterns are so unpredictable, and when you’re dependent on rain for irrigation you are affected," Chester said.
Where does Chester see sustainable cotton, both organic and other standards, in five years? “With renewed energy and excitement, both standards, organic and [Better Cotton], will scale up. Once the demand is stronger and continues to grow, farmers will see the advantage.”
That will be good for cotton farmers, for the ecosystems where they farm, and for their communities.
Image credit: Flickr/Gloria Cabada-Leman