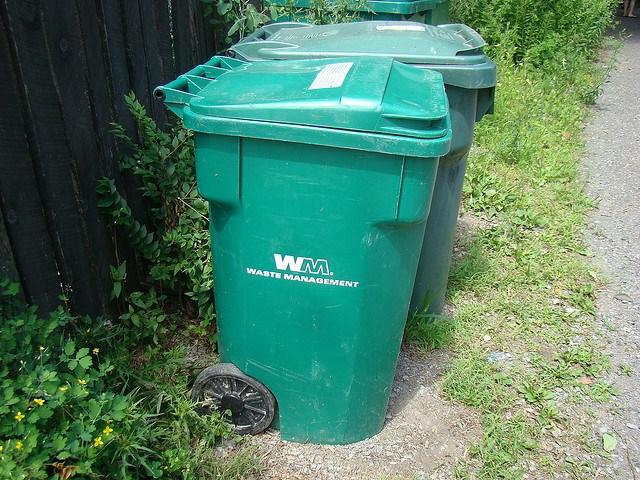
Waste Management is a company known for collecting trash. However, the company is making strides to reduce the amount of trash that ends up in landfills, as its 2014 sustainability report shows.
In 2013, WM took 15 million tons of recyclable materials from the waste stream, an 88 percent increase since 2007 and a 16 percent increase in the last two years. The company is well on its way to meet its goal of collecting 20 million tons of recyclable materials a year by 2020.
There are a variety of ways that WM is reducing waste sent to landfills. One of them is through mining: At many of its facilities, WM mines waste for cardboard and metal that can be recycled and resold. It began mining in 2011 by focusing on mining cardboard from its transfer stations. In 2013, WM focused on landfills and expanded the materials it mines. WM is mining materials at 117 of its transfer stations and 21 of its landfills.
Turning plastic into new products and energy
Plastic waste is a big problem in the U.S., where 47 million water bottles are used and thrown away every year. In 2010, WM invested in MicroGreen, a company that uses technology to turn plastics into new products. MicroGreen’s InCycle cups use up to 50 percent recycled content and are 100 percent recyclable. A lifecycle analysis by Franklin Associates found that InCycle technology requires the lowest amount of energy to create its products and produces the lowest amount of total solid waste.
WM has been developing technology to turn plastics into fuel using pyrolysis, which changes the chemical composition of organic material through exposure to high temperatures. Through pyrolysis, industrial and consumer plastics can be turned into a high octane synthetic crude oil. The crude oil is then turned into ultra-low sulfur diesel plus other transportation fuels and petroleum products.
WM’s first plastics recovery facility began its start-up phase in 2013 in Portland, Oregon. It is the largest commercially operational waste-to-plastic-to-synthetic crude oil facility in North America. It processed 848 tons of plastic into into 200,972 gallons of oil in 2013, which was delivered to a Tacoma, Washington oil refinery.
Reusing organic waste
There is much food waste and yard trimmings produced in the U.S. Combined, they make up about 28 percent of the U.S. waste stream. To reduce the amount of food waste and yard trimmings that ends up in landfills, WM created food waste collection services to over 700,000 residential and commercial customers. In 2013, WM diverted 2.4 million tons of food waste and yard trimmings from landfill to be used as compost, soil amendments and energy.
Most of the organic waste WM collects ends up in facilities that make marketable compost and soil amendment products. WM operated or was a partner with the operator of 39 organics processing facilities across the U.S. The company has also invested in several organic processors: In 2010, WM invested in Garick, a company that creates products such as compost and organic fertilizer.
Additionally, WM has invested in technologies to convert organic waste to energy, including its Centralized Organic Recycling equipment (CORe) process, which allows it to produce biogas for electricity and fuel. WM collects commercial food waste, screens it in one of its CORe facility to remove contaminants, and blends into bioslurry. That bioslurry is then delivered to municipal wastewater treatment plants, where it is anaerobically digested to increase the production of biogas. Adding only 7 percent organic material in the form of bioslurry to the plants' anaerobic digesters increases energy output by over 70 percent. The technology is still being piloted by WM, and there are projects in New York City and Los Angeles, with another one being developed in Boston.
Image credit: Neubie
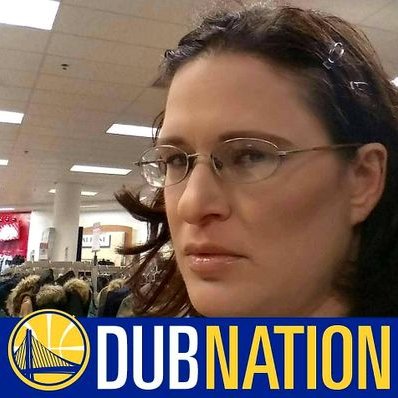
Gina-Marie is a freelance writer and journalist armed with a degree in journalism, and a passion for social justice, including the environment and sustainability. She writes for various websites, and has made the 75+ Environmentalists to Follow list by Mashable.com.