Can Young People's Faith in Democracy Be Restored?
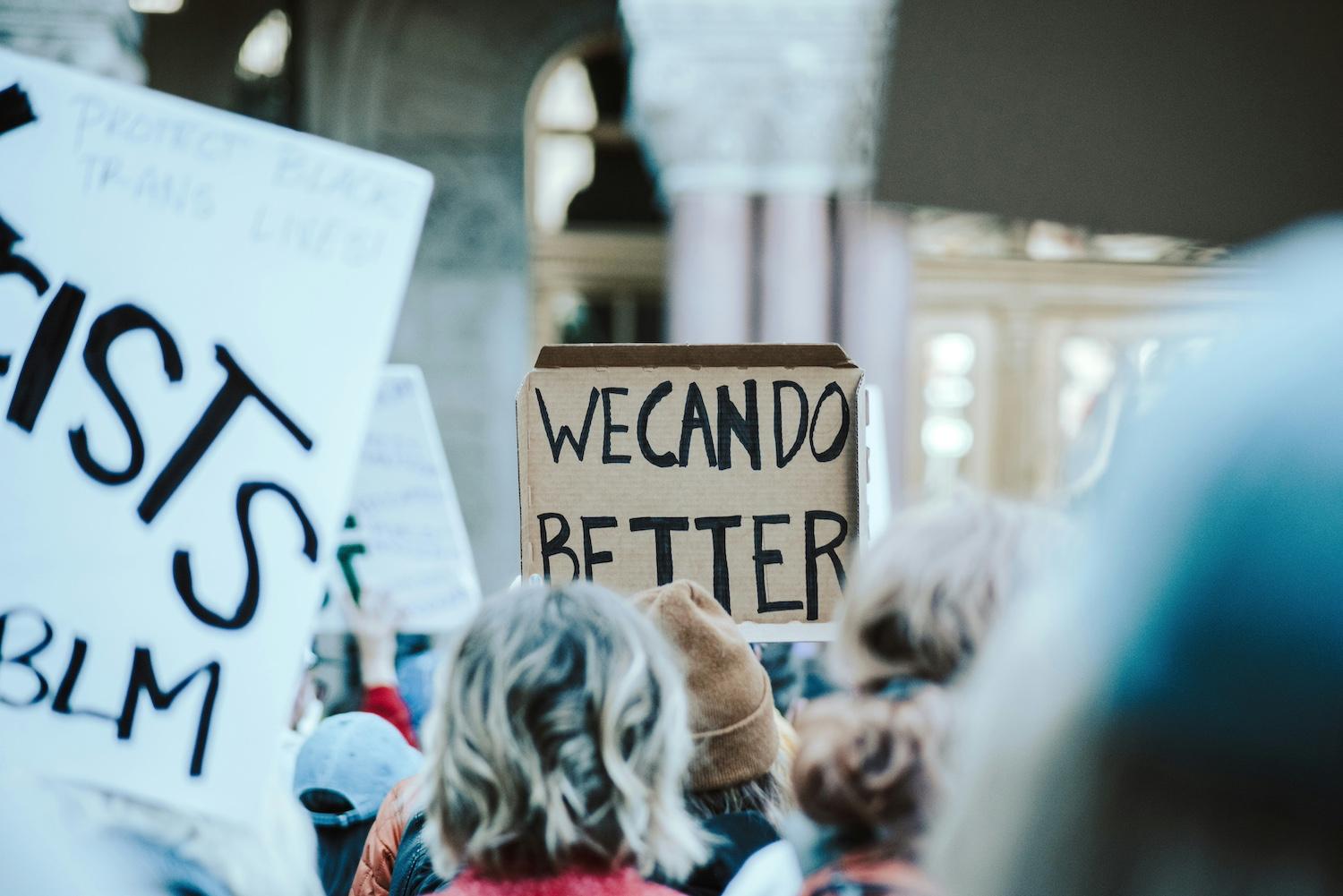
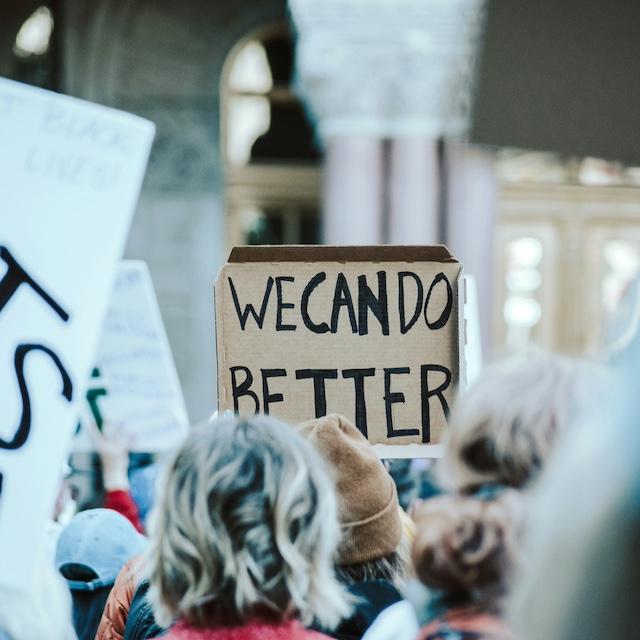
(Image: Sandra Seitamaa/Unsplash)
If you were told that over half of young people in the United Kingdom would prefer to live under a dictatorship, what year would you say this data was drawn from?
It might shock you to learn that the survey was conducted in 2022 rather than 1922.
This is the extent to which frustration has harbored among many young people who have grown disenfranchised with democracy. Those who see only a widening disconnect between the priorities of current leaders and their own.
Young people are increasingly viewing the efforts of global leaders as incapable of turning the dial on the issues that mean the most to them, notably the climate crisis, economic insecurity, mental wellbeing and social inequality.
This is a generation set to inherit a world where climate change nears a point of no return, where inequality is skyrocketing and mental health plummeting globally. Inaction — or at least insufficient action — is driving a cohort of voters away from democracy.
With almost half of the world's population voting in 2024, how can we restore faith in a system that has failed young people and their concerns?
Better engagement with the issues that mean the most to young people
Young people are often overlooked in political processes. For example, 60 percent of Africa’s population is aged under 25, but the median age of its leaders is 62, according to the nonpartisan research nonprofit the Brookings Institution. If politicians want young people to engage, they need to engage with the issues that matter to them.
Young people are particularly invested in social inequality and climate change, with 51 percent of those polled by the global community for young leaders One Young World saying that climate anxiety was negatively affecting their mental health and 55 percent saying that they had no confidence in those leaders to deliver net zero by 2050. When we look at the polling numbers for incumbent leaders, it becomes clear that current politicians are not addressing these issues effectively, if at all.
This is evident in the United States, where President Joe Biden’s approval ratings have dropped significantly amongst young voters primarily due to his stances on issues important to them — namely inaction over student debt and climate change. Young people globally are growing increasingly impatient with global leaders and their inability to turn the dial on such issues.
Take for instance the response to the Grenfell Tower fire. Just last month we were told that the final report of the tragedy was further delayed and wouldn't be published until after the seventh anniversary of the disaster. Now compare it to Russia’s swift response to the mall fire that killed 64 people in Kemerovo, where managers faced charges just days after the blaze. Russian authorities face accusations of corruption and misleading the public, but where there is public anger, there is a lack of patience with institutions and a disregard for due process.
And with this atmosphere of public anger and impatience, the false promise of the autocrat becomes an ever present threat: That strong-man leaders move decisively, whilst the focused deliberation of democracies is inherently slow.
If incumbent leaders wish to engage young people, they need to listen to their concerns and commit to tangible action, and they need to move faster. Young people’s priorities, such as housing and climate change, cannot afford more decades of inaction.
Empower the next generation of young leaders to secure democracy
Whilst those currently in power need to listen to the concerns of young people, the security of democracy depends upon the next generation of leadership. It is imperative that we cultivate strong, ethical and self-aware leaders that are equipped to face the challenges of rising authoritarianism.
Part of that process must be empowering young people to play a more central role in decision making, allowing them to address the concerns of their peers and introducing new perspectives into traditional institutions.
In order to make lasting change, youth voices need to be included for policies to respond to the specific needs of younger generations, according to the Electoral Knowledge Network.
In many parts of the world we have seen a hopeful start to this trend. From France electing their youngest prime minister, Gabriel Attal, at age 35, to Ireland’s new taoiseach, Simon Harris, aged 37.
We must give recognition where recognition is due. That’s why in 2018 we created the One Young World Politician of the Year Award. It is the first global award to recognize the most promising young politicians between the ages of 18 and 35 from around the world using public office to effect positive change in their communities, particularly to benefit and represent young people. The 2023 winners included: Arielle Kayabaga, member of parliament for London West, Canada; Moko Tepania, mayor of the Far North District, New Zealand; Sobita Gautam, member of the House of Representatives, Nepal; and Ayor Makur Chuot, member of the 41st Parliament of Western Australia.
But leadership is not just about politics, and young people should be trusted in other spheres of influence as well. From business and community leaders to innovators, young people have shown that they have a vested interest in tangible solutions, and we must enthusiastically empower their endeavors.
In order for young people to have trust in democracy we must trust them, by inviting them to the table, platforming their voices and investing financially in their ideas.
Create forums for collaboration
As the world becomes increasingly more polarized, and young people continue to become more skeptical and more detached from society, the importance of creating community is clearer than ever. We face some of our most global and existential challenges, from climate change to rampant inequality. If we are to effectively tackle these issues, we must work together.
Investing in spaces for like-minded individuals to come together and work towards common goals is crucial. Each year at the One Young World Summit, I see the tangible progress that grows from conversations and connections at the event. International forums for collaboration act as a key means to engage and inspire younger generations, empowering them to find an active role in the betterment of society.
But beyond this, these forums create the space to bridge divides and debate contrasting opinions.
Listening to and understanding contrasting perspectives, and even criticism, can open up your world view and allow you to strengthen your resolve and mission. Understanding why people are resistant to the change you are proposing allows you to adapt your proposition and give your cause a better chance at acceptance. As One Young World Counselor, Thuli Madonsela, who helped draft the South African constitution, says, “seeking first to understand the world view and concerns of those who disagree provides a basis for establishing some common ground."
While there might be a crisis of faith in democracy, it is clear as to why. Young people feel as though they do not have a seat at the table and are powerless to make change. Our current leaders must do more to engage on the issues that matter most to young people and ultimately we must empower and champion our young leaders to take on leading public roles. Collaborative forums where young people can engage with current global leadership as well as like-minded individuals is essential to inspire the next generation of change makers.
It’s also important to recognize that young people are already changing the world and making steps towards a fairer and more sustainable future. If we truly want to dispel the false promise of the autocrat and restore faith in democracy, we must trust young people to do this not just "tomorrow," but now.