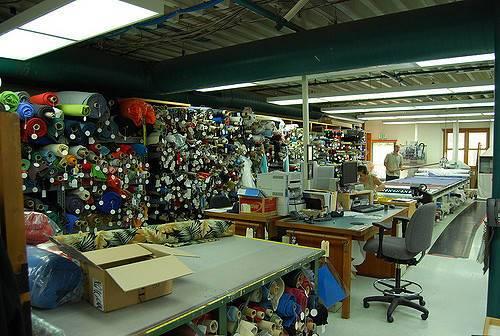
By Laura Quinn
When the 1990s brought to light a series of corporate exposés and Naomi Klein’s anthem for brand mistrust, No Logo, was published, the role of brands in perpetuating “sweatshop” conditions in the supply chain was thrust vividly into public consciousness. As a watershed moment, clothing retailers across the world have been on an upward curve to make swift and visible changes to their sourcing strategies ever since. CSR programs, compliance audits, and collaborative NGO partnerships have helped to improve conditions factory by factory, while flagship agreements like the Bangladesh Accord, combined with voluntary social standards like the Higg Index, have created new levels of benchmarking.
But, despite the plethora of initiatives, indentured labor, poor safety records, harassment, and inadequate wages are still commonplace within almost every producing nation, leaving garment workers paying the price for the world’s fast-fashion obsession. Corporate responsibility teams have so far struggled to sufficiently influence market dynamics and drive change at scale across the complex network of manufacturers and sub-contractors within the global garment sector.
That’s where a new breed of researchers and academics are stepping in. By proving that improved worker welfare leads directly to increased profitability, researchers are demonstrating that better conditions are not only the right thing to do, but a profitable business decision for manufacturers. Such evidence has the potential to transform the argument for greater responsibility in the garment supply chain - from an abstract moral imperative to a concrete business opportunity. And it might just hold the key to the kind of scalable improvements we’ve been striving for over the last 30 years.
Better Work is one such organization, a collaboration between the United Nation’s International Labour Organization (ILO) and the International Finance Corporation (IFC). It was established specifically to improve working conditions and worker rights, while boosting the competitiveness of the apparel industries. Working with academics from Tufts it was able to show conclusive benefits to productivity – and profitability – for manufacturing businesses from its three-day Supervisory Skills Training course. Through the program, factory supervisors were found to be more empathetic to the needs of workers and retention levels for both supervisors and workers improved, while injury rates went down. Most encouragingly, supervisors reported their lines reached targets 11 minutes faster, an estimated 22 percent increase in productivity.
Similar results were discovered by academics from the Good Business Lab, when they began studying the business impact of Gap’s P.A.C.E program on factories in India several years ago. The program aims to advance the lives of female workers through soft skills training, from which Gap had already seen positive impacts including increased self-confidence, better communication skills and a higher likelihood of getting promoted. Taking into account the cost to train the women, the academics undertook a randomized controlled trial (RCT) and found a direct return on investment of 124 percent by the end of the program and 420 percent nine months later – meaning the manufacturer was actually making a profit by implementing the program.
Focusing on HR and productivity training, Impactt’s Benefits for Business and Workers (BBW) program aims to prove that better pay and working conditions for workers leads directly to improved productivity and profit. In 2016, Impactt was able to measure the impact of the program’s second phase across 88 factories in Bangladesh. It found that, through better pay and working conditions, factories collectively gained £6.9m in profit, while 243,134 workers received an additional £6.2m in pay.
The results are, as yet, small samples and the findings reside largely in the world of NGOs and academia. The next challenge will be to bring these findings to manufacturers across producing nations, providing compelling financial data and simple templates that enable them to replicate the results in their own factories. If we can engage, educate and inspire every manufacturer to understand the financial value to them from improved conditions, then we could be looking at the start of a self-sustaining transformation across the garment industry - built on a solid economic foundation, and supplemented by continued campaigning on the moral imperative to improve the lives of garment workers.
Laura Quinn is a sustainability communications consultant specializing in the garment industry, and founder of Indian consulting firm Do One Thing.
TriplePundit has published articles from over 1000 contributors. If you'd like to be a guest author, please get in touch!