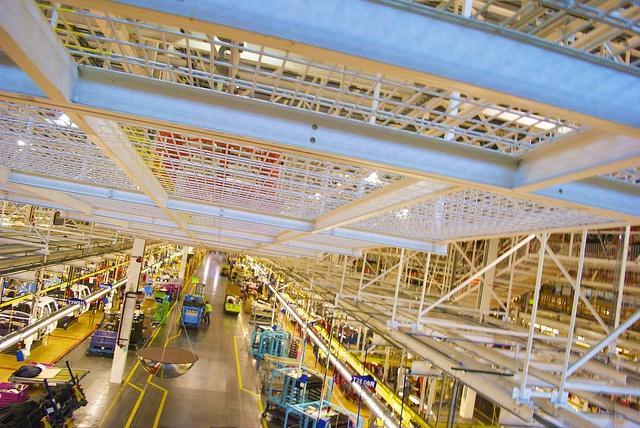
It taught us to fly. It revolutionized our fastest land travel. And it taught us how to keep our pants from falling down without a zipper or a button.
Biomimicry -- using nature to find solutions to the world's most challenging or creative questions -- has been in force for centuries. A 19th-century Catalan architect, Antoni Gaudi, looked to the canopy structure of trees to build the Spanish church La Familia Sagrada in Barcelona. The Wright Brothers mimicked birds in order to teach themselves how to become airborne. Japanese bird-enthusiast and engineer Eiji Nakatsu used the unique design of the kingfisher's beak to figure out how to pierce the atmosphere with maximum speed, leading to the Shinkansen Bullet train. And of course, the mimicry you might not have expected: Swiss engineer George de Mestral's use of the burdock burr in the 1950s to figure out how to create what eventually became known as Velcro.
Today, biomimicry is a studied science and recognized as an asset for numerous applications. The most recent to be considered, however, strikes at the very issue we seem most concerned with these days: reducing our waste stream. Ford Motor Co. has found an unusual ally in its efforts to divert waste and increase the reuse-potential of its car parts: the gecko.
The tiny, web-footed reptile has an unusual secret that scientists would like to get to the bottom of: how its sticky toe pads allow it to climb and maintain its grip on surfaces without liquid or other residues that could interfere with its agility. Figuring out that question, says Ford, might help the company discover how to assemble parts without the use of glues and foams.
The adhesives currently used in automobile construction pose a real problem when it comes to breaking down decommissioned parts for recycling. Breaking apart machinery, casings and other parts makes recycling a challenge in some cases, but so does the actual adhesive, which may not be able to be recycled with the metal.
"Solving this problem could provide cost savings and certainly an environmental savings,” said Debbie Mielewski, Ford's technical leader in plastics and sustainability research. “It means we could increase the recycling of more foam and plastics, and further reduce our environmental footprint.”
And Ford isn't the only one that will benefit from this research. Procter & Gamble plans to pair up with the automaker. Figuring out how to create an adhesive surface without using potentially toxic glues and other adhesives could benefit both companies.
Their efforts in this arena will also benefit the goals of the nonprofit Biomimicry Institute, which wants to encourage the use of biomimicry in current applications. For its part, Ford seems to be on board with that aim. The automobile manufacturer recently hosted a forum on biomimicry that was attended by more than 100 designers and scientists looking for ways to solve sustainability challenges with a little help from Mother Nature's most ingenious inspirations.
Image creditss: 1) Frank Vassen; 2) Nichole Yeary
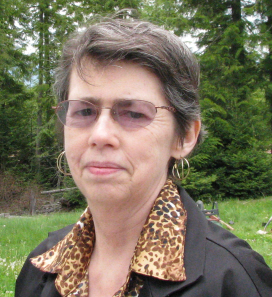
Jan Lee is a former news editor and award-winning editorial writer whose non-fiction and fiction have been published in the U.S., Canada, Mexico, the U.K. and Australia. Her articles and posts can be found on TriplePundit, JustMeans, and her blog, The Multicultural Jew, as well as other publications. She currently splits her residence between the city of Vancouver, British Columbia and the rural farmlands of Idaho.