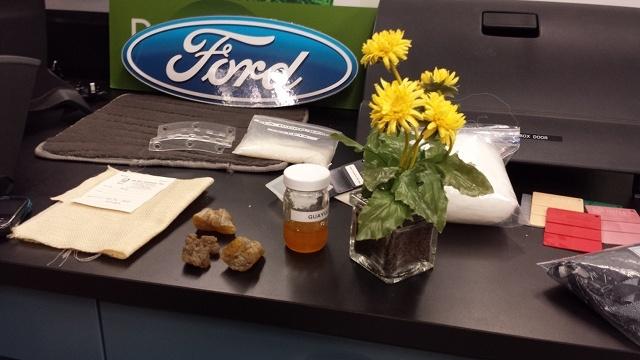
Researchers at Ford Motor Co. have been working to replace petroleum-based plastic with renewable alternatives for nearly 15 years. Back in 2000, Debbie Mielewski, senior technical leader for sustainable materials at Ford Research, and her team devised a chemical formula to replace petroleum-based automotive foam with foam made from soybean oil.
It wasn't always easy. As Mielewski explained to a group of journalists in the research lab last week, the first soy-based foam the team tested was "the most miserable, stinky, terrible foam ever. It smelled like burnt popcorn."
But, she continued, the team had plenty of time to perfect the formula. Why? To put it bluntly: because the rest of the company wasn't expecting much anyway.
"Way back in 2000, people said: 'Why the heck do you want to do this? Petroleum is cheap; we've been doing it for 50 years with the petroleum-based chemicals. Why would we want to change it?'" Mielewski recalled that she and her colleague Ellen Lee were "thrown out of every conference room in the whole company."
As the researchers continued their work, it often seemed as if the department wouldn't live to see the results. But, in the innovative spirit of his great-grandfather, Executive Chairman Bill Ford wouldn't hear of it. "Every time the project was about to be shut down due to resource constraints, we would hear from behind the scenes that Bill Ford met with somebody and that we were going to keep going," Mielewski said.
Finally, after years in the laboratory, the team's hard work paid off. In 2007, Mielewski, Lee and their colleagues completed a soy-based foam that met every specification Ford had in place for its automotive foam. "That's when the magic sort of happened for us: Oil went from $40 a barrel to over $160 a barrel," Mielewski continued with a smile. "The phones started ringing off the hook, and they said, 'You know that really crappy idea? That's a good idea.'"
The company first rolled out its soy-based foam in the 2007 Mustang. Although Mielewski worried that speed-loving Mustang enthusiasts may not "want beans in their seats," both customers and the media quickly fell in love with the concept. "That sort of spurred us on to keep going," she said.
Fast forward to today: Ford has since rolled out soy-based foams to every vehicle it makes in North America -- saving 1.5 million pounds of oil annually. Around 85 percent of all headrests across the Ford line now contain soy foam. "We're migrating it out, and that was the whole intent," Mielewski said. "You don't want to develop one of these materials if you're not going to use it extensively and actually do good for the environment."
The company is looking to expand its use of soy foam to door panels, steering wheels and carpet insulation, Mielewski said. "If it can be done for seat cushions and backs, it can probably be done for all the other applications as well."
The 'growth' of renewable materials at Ford
With the soy foam perfected, the plastics research team had no plans to slow down -- and the company has since developed and launched eight plant-based materials for use in its car parts.
"We're trying to, in all cases, substitute things we can grow for these petroleum-based materials that are not sustainable and not good for the planet," Mielewski said. "When you use a plant, the really cool thing is: While the plant is growing it's taking in CO2, so we're reducing greenhouse gas emissions every time we use a plant."
Introducing natural materials is helpful in more ways than one: "The nice thing is that not only are they based on renewable resources that you can grow but they're a lower density than talc or glass fiber," said Ellen Lee, team leader for plastics research. "So, in the end the composite material is lighter in weight, which helps us additionally with fuel economy."
In addition to soybean oil, here are a few other renewable materials Ford uses to supplement petroleum, as well as glass and mineral reinforcement agents, in its plastic parts:
- Wheat straw: Wheat straw, a byproduct of wheat production that is typically discarded or burned, is used to replace the glass fibers or minerals commonly used to reinforce plastic parts. Wheat straw-based plastics were rolled out in the Ford Flex in 2009, with additional applications under development.
- Kenaf: Kenaf, a tropical plant in the cotton family that looks similar to bamboo, replaces oil-based resin in plastic door interior bolsters on the Ford Escape. The use of kenaf in vehicle door bolsters offsets 300,000 pounds of oil-based resin per year in North America.
- Guayule: This Southwestern plant is under development as a rubber and latex alternative. The company is also looking to dandelion root for its similarly rubber-like properties.
- Coconut fiber: In North America, Ford uses a coconut-fiber trunk liner in its flagship electric vehicle, the Focus Electric.
- Rice hulls: A composite plastic material reinforced with rice hulls was introduced in the wire harness of the 2014 Ford F-150. The rice hulls, which are a byproduct of rice grains, are sourced from farms in the U.S.
- Cellulose: An industry first application of cellulose-reinforced plastic was introduced in the 2014 Lincoln MKX. This material, sourced from sustainably harvested trees and related byproducts, is being used to replace fiberglass reinforcement in the center console.
- Retired currency: An estimated 3.6 million pounds of retired U.S. currency is shredded every year, and Ford has bright ideas for the Treasury Department's discards. The company's research team is currently developing ways to use shredded currency to reinforce plastic in components like, fittingly enough, console coin trays.
Forging partnerships for a more sustainable future
While Ford is making significant strides on its quest to "grow" its own car parts, the company doesn't plan to embark on its journey alone. Back in 2012, Ford joined with four other leading companies -- Coca-Cola, Heinz, Nike and Procter & Gamble -- in a strategic working group to ramp up the development of bioplastic.
The cooperation had its foundation in Coca-Cola’s PlantBottle, a PET product the beverage giant released in 2009 that is partially manufactured out of plant-based resins. Coca-Cola licensed the product to Heinz a year earlier, and both Nike and P&G also plan to use it in products and packaging. Ford researchers are now working with Coca-Cola to adapt the technology for use in vehicle fabrics, and a demonstration vehicle with PlantBottle-based interior fabrics went on display late last year.
But that's not the only way the partnership is driving innovation in alternative materials: Earlier this year, Ford and Heinz announced that they would work together to transform tomato scraps left over from the ketchup giant's manufacturing facilities into bio-based plastic.
Mielewski jokingly recalled the light-bulb moment when she and CEO Alan Mulally were chatting with some executives at Heinz. After the Heinz folks complained about the excess tomato fiber heading to landfills from their plants, Mielewski and Mulally looked at each other and said, "We can do something with it."
Ford's research team is currently testing these tomato scraps, made up of peels, stems and seeds from the more than 2 million tons of tomatoes Heinz uses annually, for plastic reinforcement. The ultimate goal of the five-company-strong partnership is to develop a 100 percent bio-based plastic.
“We are delighted that the technology has been validated," Vidhu Nagpal, associate director of packaging R&D for Heinz, said earlier this year. "Although we are in the very early stages of research, and many questions remain, we are excited about the possibilities this could produce for both Heinz and Ford, and the advancement of sustainable 100 percent plant-based plastics."
While we're surely a long way away from "growing" the plastics we use in our daily lives, the research underway at companies like Ford is slowly bringing us closer to achieving that goal. Considering the fact that Ford alone uses about 300 pounds of plastic in every vehicle it manufactures, one thing is for certain: Every little bit helps.
Images by Mary Mazzoni
Editor’s Note: Travel accommodations for the author and Triple Pundit were provided by Ford.
Based in Philadelphia, Mary Mazzoni is a senior editor at TriplePundit. She is also a freelance journalist who frequently writes about sustainability, corporate social responsibility and clean tech. Her work has appeared in the Philadelphia Daily News, the Huffington Post, Sustainable Brands, Earth911 and the Daily Meal. You can follow her on Twitter @mary_mazzoni.
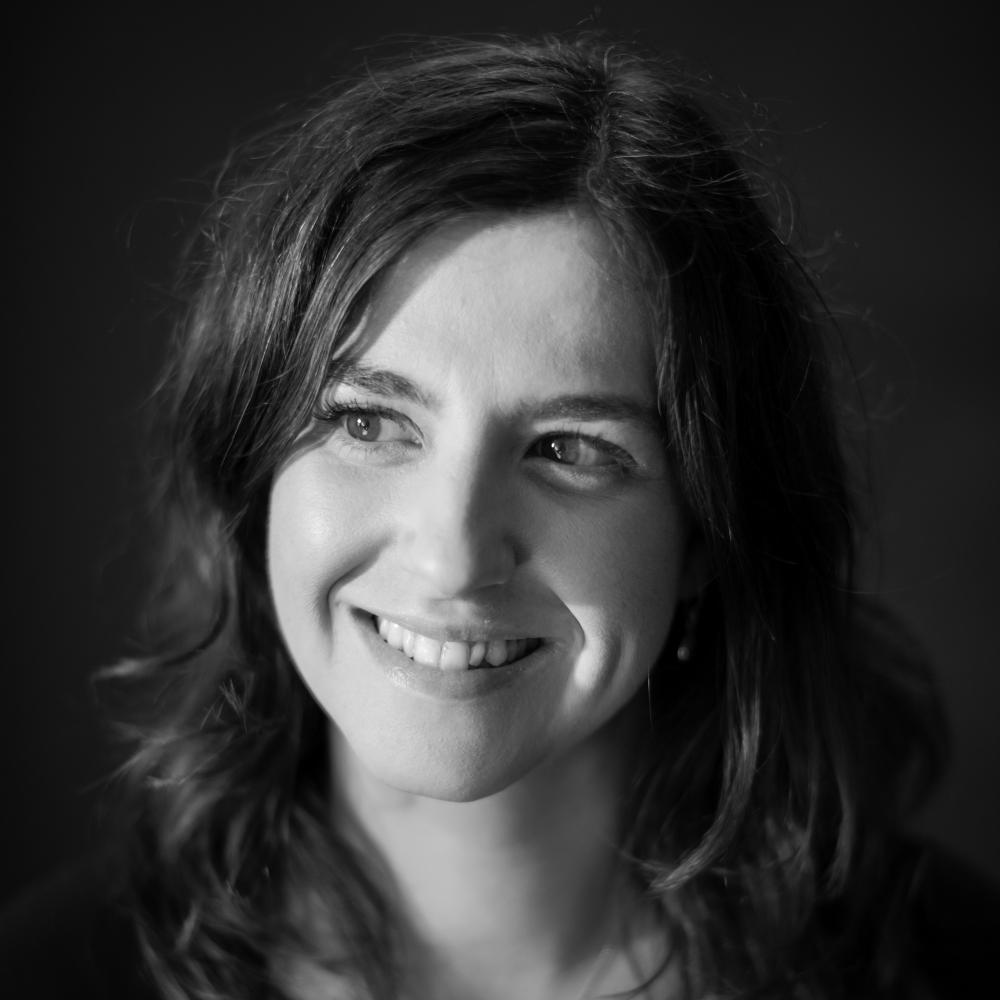
Mary has reported on sustainability and social impact for over a decade and now serves as executive editor of TriplePundit. She is also the general manager of TriplePundit's Brand Studio, which has worked with dozens of organizations on sustainability storytelling, and VP of content for TriplePundit's parent company 3BL.